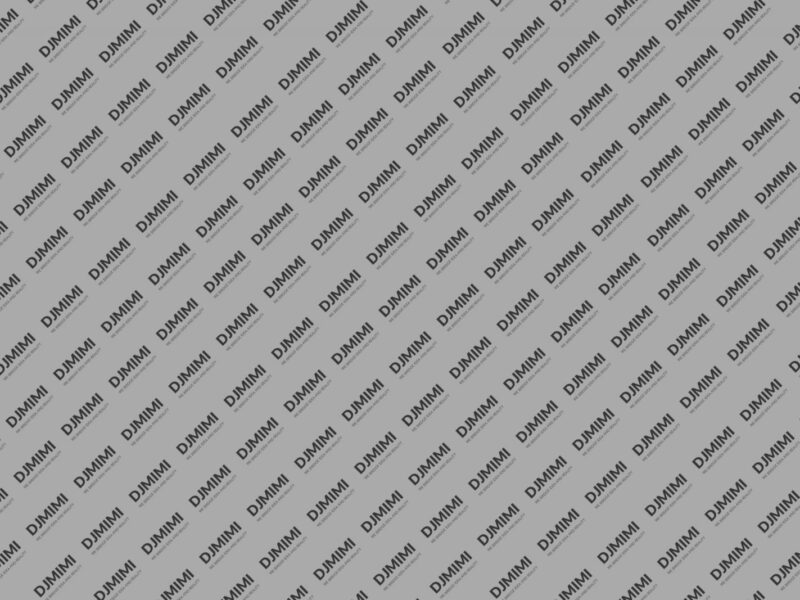
[vc_row css=”.vc_custom_1455531352097{margin-bottom: 15px !important;}”][vc_column][vc_column_text]Petroleum refining processes are the chemical engineering processes and other facilities used in petroleum refineries (also referred to as oil refineries) to transform crude oil into useful products such as liquefied petroleum gas (LPG), gasoline or petrol, kerosene, jet fuel, diesel oil and fuel oils.
Petroleum refineries are very large industrial complexes that involve many different processing units and auxiliary facilities such as utility units and storage tanks. Each refinery has its own unique arrangement and combination of refining processes largely determined by the refinery location, desired products and economic considerations.
Some modern petroleum refineries process as much as 800,000 to 900,000 barrels (127,000 to 143,000 cubic meters) per day of crude oil.
Auxiliary facilities required in refineries
- Steam reforming unit: Converts natural gas into hydrogen for the hydrotreaters and/or the hydrocracker.
Sour water stripper unit: Uses steam to remove hydrogen sulfide gas from various wastewater streams for subsequent conversion into end-product sulfur in the Claus unit. - Utility units such as cooling towers for furnishing circulating cooling water, steam generators, instrument air systems for pneumatically operated control valves and an electrical substation.
Wastewater collection and treating systems consisting of API separators, dissolved air flotation (DAF) units and some type of further treatment (such as an activated sludge biotreater) to make the wastewaters suitable for reuse or for disposal. - Liquified gas (LPG) storage vessels for propane and similar gaseous fuels at a pressure sufficient to maintain them in liquid form. These are usually spherical vessels or bullets (horizontal vessels with rounded ends).
Storage tanks for crude oil and finished products, usually vertical, cylindrical vessels with some sort of vapour emission control and surrounded by an earthen berm to contain liquid spills.
[/vc_column_text][/vc_column][/vc_row]