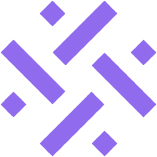
Evolution of Marking Machines: Use of more and more machines in manufacturing led to mass production of parts and soon a need was felt to identify and trace those manufactured parts that were part of critical engineering assemblies. This required each manufactured part to be marked uniquely. In early days, this was done manually by use of marker pens and later by manual stamping of letters and numbers. As the capacity of mass production systems increased, the marking process also needed to be speeded up. Thus a machine operated stylus to make tiny dot-indents on metal surface was developed. This system used tiny dots to form letters and numbers and was named dot peen marking. Over the years, the speed of marking and its accuracy were improved and later this marking machine was integrated to the production line, to further improve productivity of marking.
Other systems of marking like subscribing, which is an engraving type of marking, and laser marking were also developed. Apart from improvements in marking technologies, customized solutions were created when the parts were not identical in size or surface level. Portable and autonomous marking machines also came into being for large parts such as automotive chassis, gearboxes etc
Development of Marking Systems Over the Years: When we talk of future of any equipment or machinery, we need to first look at its development in the context of technology, products and new applications and customization. Let’s look at each of these in case of marking machines.
Marking Machine Technology: Dot Peen Marking: The technology employed here is simple electro-mechanical movement whereby a diamond stylus moves back and forth, when pulse current is passed through a solenoid. As this stylus hits a metal surface, it makes a small dot-shaped indent. These tiny dots are used to create letters, numbers, and even an image. With improvement in technology, the size of the dot has progressively become smaller and more accurate, and the speed of marking has improved manifold. New age dot peen machines can now print a dot-matrix image, which can be read and verified by a camera and a computer system.
Scribing : In this type of marking, a carbide or diamond tip penetrates the surface and makes a groove. The marking therefore is in the form of a continuous line or a continuous groove. This is also called “drop and drag” or “scratch” marking. The fundamental advantage of this marking is low-noise operation as compared to dot peen marking. This type of marking works well with optical character recognition. Most of subscribing marking machines use pneumatic movement for the marking tip.
Laser Marking: Laser is a high energy beam of monochromatic light, which can penetrate even a metal. For marking application, a high frequency beam is generated from a laser source and is then amplified in a fiber optic cable, and focused using a series of rotating mirrors. A lens then concentrates this beam into 30 micro meter size. When this laser beam hits a metal surface, three distinct reactions take place –engraving, annealing, and foaming. While engraving creates a groove, annealing changes material color at the groove. Foaming alters the coating at the surface. A fiber laser has proved to be a reliable and low maintenance option for marking.
Products: Column Mounted Marking Machine
The most commonly used machine for off production line marking of parts is column mounted machine. Most prominent in this category is the dot peen type marking machine. These Machines can mark up to 3,000 parts per day, with an accuracy of 0.02 mm. These machines can mark parts of different shapes and surface conditions like flat, concave, convex, or circular. Different marking types can be stored as software and can be downloaded from a PC onto the machines controller, using USB key. Using different software; linear, angular, radial, and mirror-image marking is possible. The software also incorporates self-diagnostics and machine-history functions.
Some column mounted machines are laser type as well. These machines are primarily used for direct part marking or label marking, which require greater accuracy. Software is used to steer the laser beam for different type of marking.
Portable Marking Machines: Portable marking machine is needed when the job is large in size. These machines are robust, easy to operate, and highly mobile. Many of the portable machines are battery operated and can mark on materials from plastics all the way to hardened Steel of 62 HRC. These machines have a built in keyboard and integrated software.
Integrated Marking Machines: These machines can be integrated on the production line using Ethernet, Profinet, or Profibus. The marking machine could be dot peen or laser type. Some of these machines are like “plug and play” with use of RS 232 interface and USB for communication with a PC. Such machines are intelligent and very versatile. These can be set up very easily by a machine operator and do not require intensive training to setup or operate. Marking head for integrated marking systems could be laser, dot peen or scribing type.
Customized Solutions and Innovations: While in most applications it is possible to simply plug-in an integrated marking machine on to the production line or mark large number of parts offline using a column mounted marking machine; there are some applications that need customization. For instance, to mark a shaft with varying length and diameter at its end, it may need customization in the form of fixtures to hold the shaft in vertical or horizontal position. Surface detection is done by use of sensors. Similarly, to mark three different sizes of plates will also need customization. Here, plate-feeders of different size are made and marking cycles are designed accordingly. In another example circular marking on screw heads of different head-diameters is achieved using motorized axis on a pneumatic actuator. Screws are held in place using pneumatic clamping. Motorized axis and pneumatic actuator help in saving marking cycle time. Customization in integrating marking machine on a production line is also feasible. For instance, laser marking on cylinder heads, bearing caps and cast-aluminum crank cases.
Among innovations, data matrix and automated vision solution is prominent. It is essentially a “mark and check” system which offers an effective traceability system. Here the marking is in the form of data matrix code. To verify the quality and readability of this mark, a vision system using camera is employed. Thereafter verification is required to be done wherein the data matrix reading is compared with specified parameters or metrics defined by ISO standards. Such a mark and check system ensures that there would be no errors in identification and traceability.
Future of Metal Marking Machine: Taking into account the prevailing technology, the products in use, and possibilities of customized solutions; it may be possible to speculate marking machine of near future. With production lines becoming progressively more automated and increased use of robots, there would be greater challenge in integration. Even as an incremental improvement is likely in marking speeds, finer and smaller marking will be preferred in future. This will need more focused laser beam and greater flexibility and speed of beam steering. Low cost and low maintenance laser marking systems will be preferred in near future.
To work with robots, integration would require more accurate sensors for positioning, and more complex actuators, which could work in sync with robots.
Of course, there would be greater emphasis on mark and check system for more and more applications. This means data matrix codes would be marked on the surface of more and more parts. System of verification, reading, and communication would become more widespread. This would need low cost and compact hardware.
So, the marking machine of 2020 would be an integrated laser type mark and check system, with a compact and low-cost vision hardware; operating along with robots and a complex system of clamping devices, sensors, and actuators.